Industries We Serve
We've built and installed thousands of waterjet machines across a diverse industry portfolio to suit specific manufacturing and material cutting needs.
30+
Years OF WATERJET EXPERIENCE
40+
waterjet accessories
100+
million waterjet combinations
Products We Sell
Our modular products can be tailored to fit your needs and provide a perfect solution to your challenges.
Abrasive Systems
Water Only Systems
Custom Waterjets
Our Companies
WARDJet is part of AAG Tailored Cutting Solutions. We are global leaders in modular CNC technology with a vast technical support network.
Partnerships
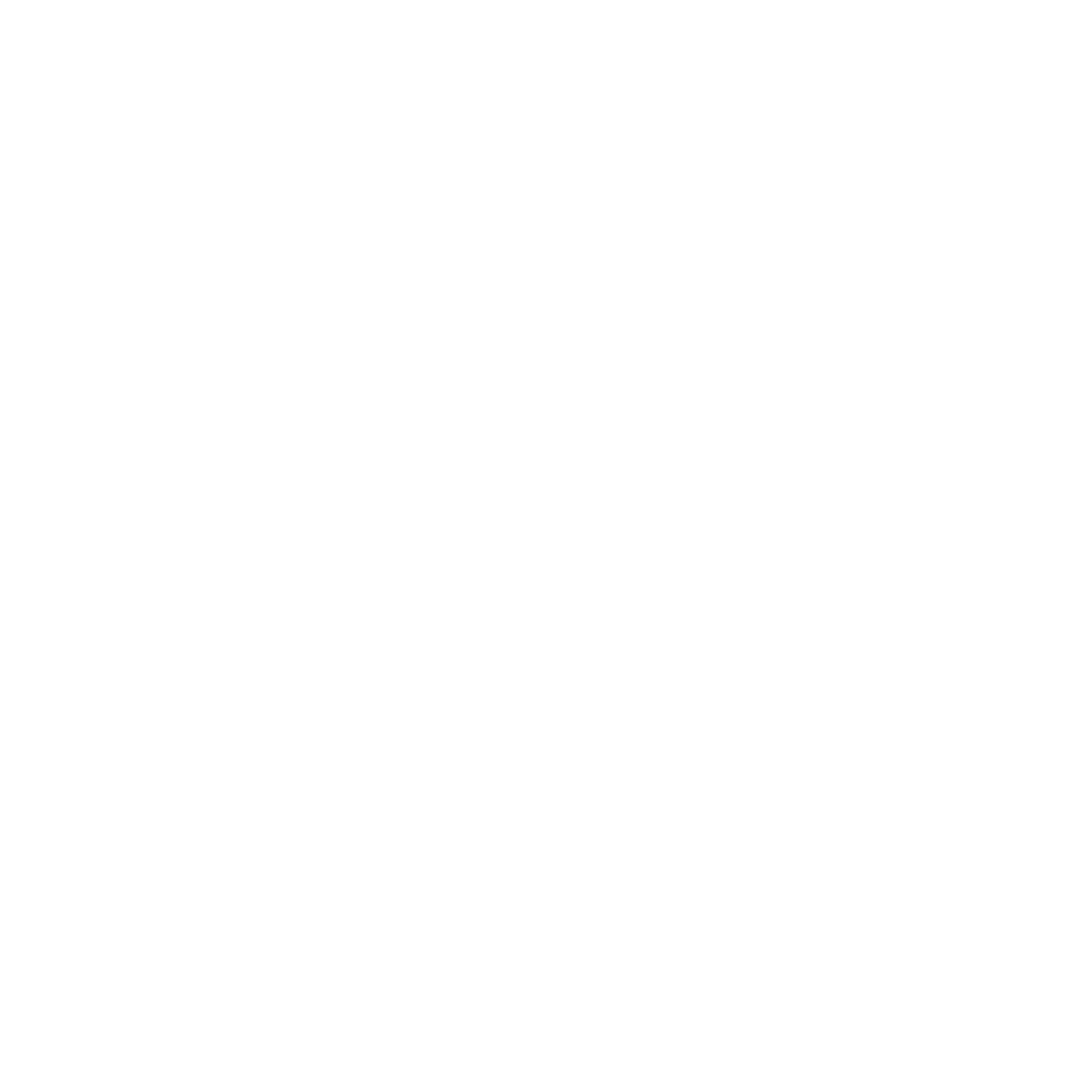
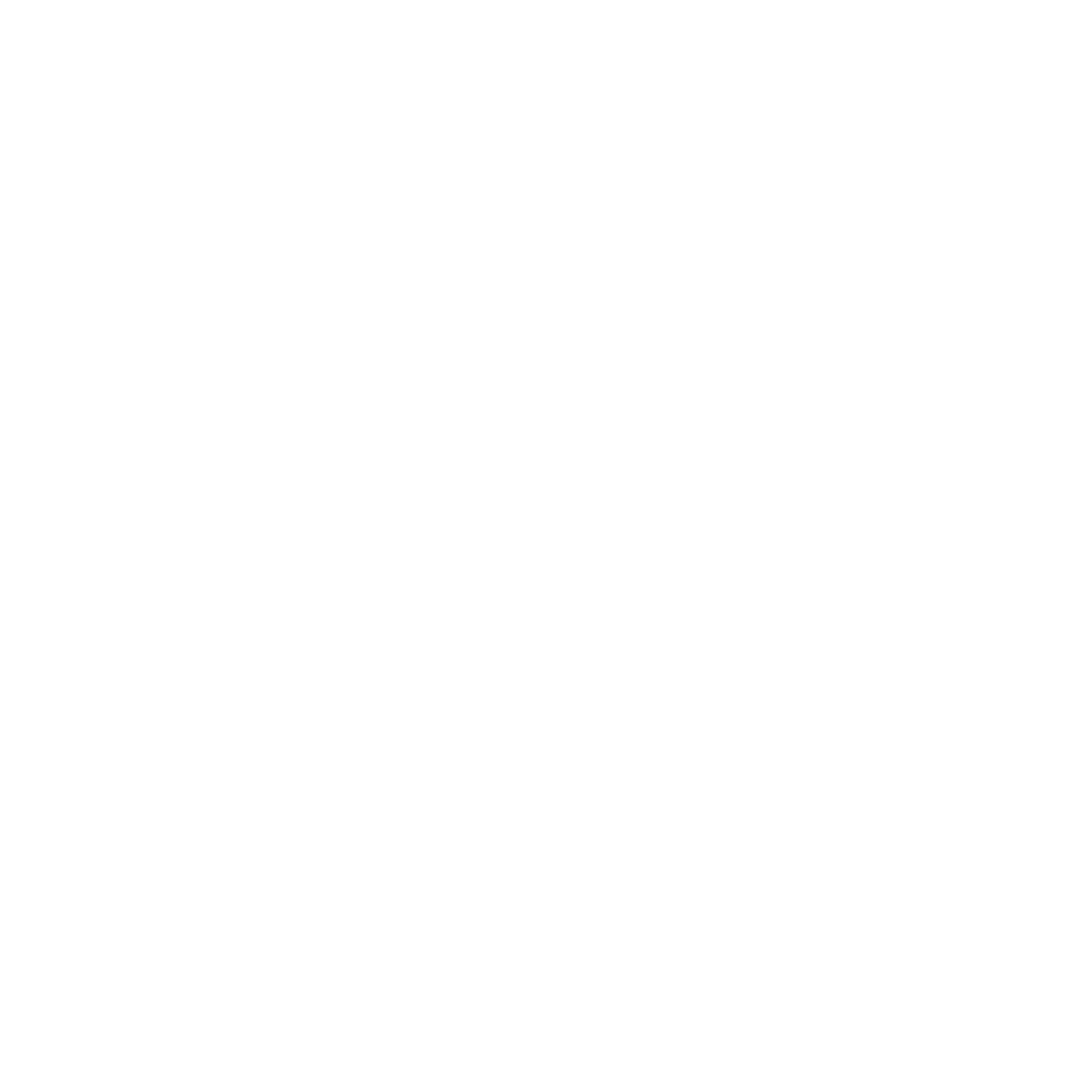
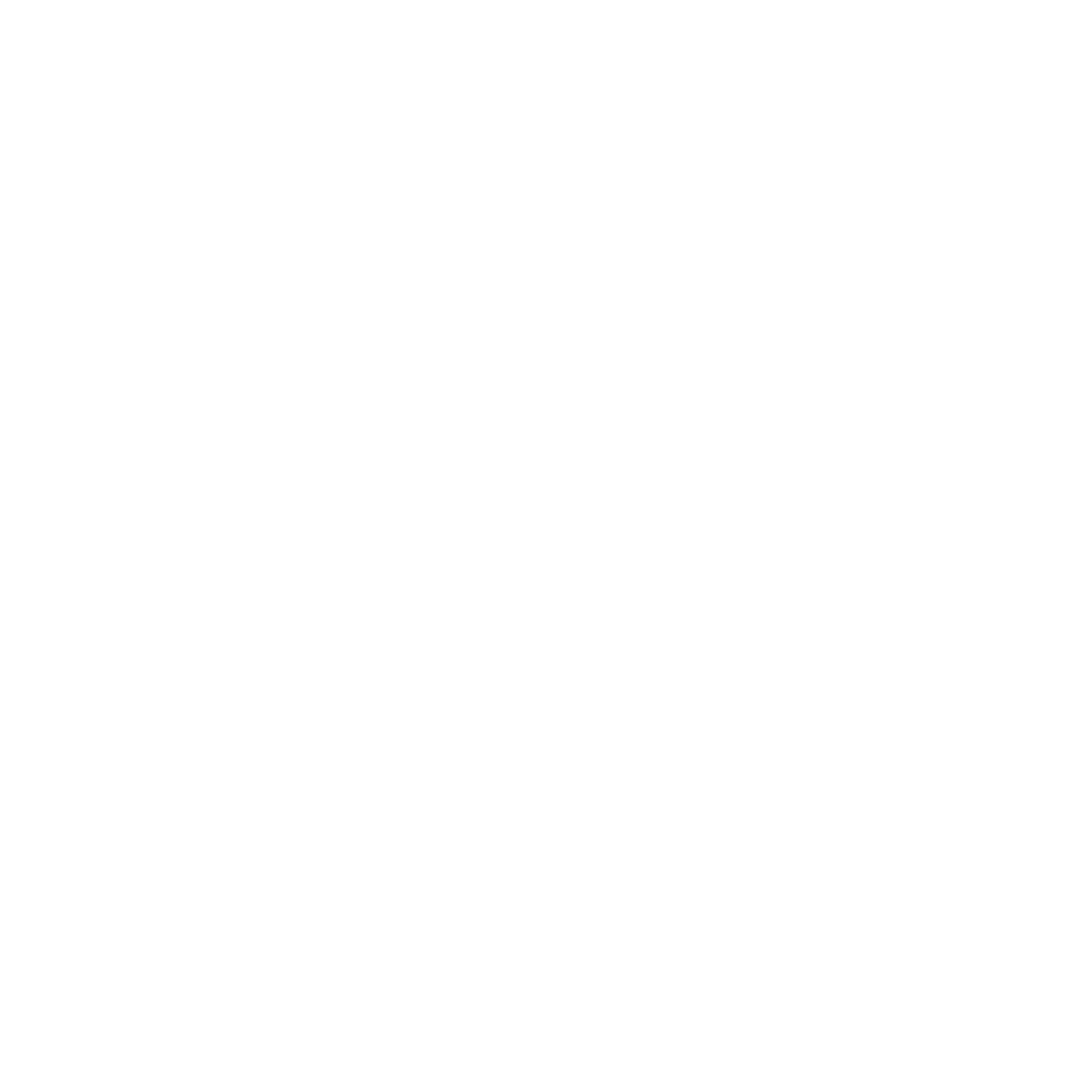
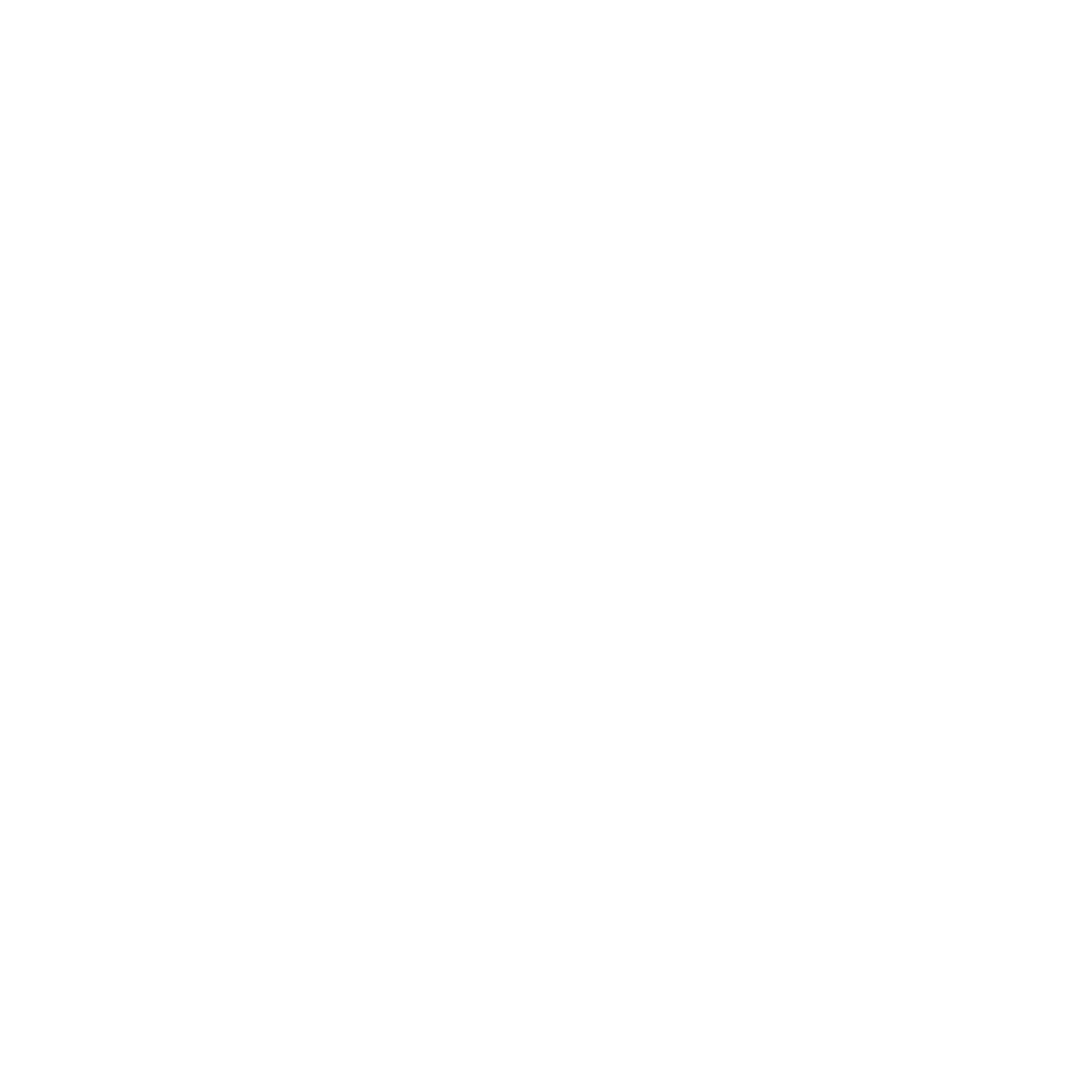
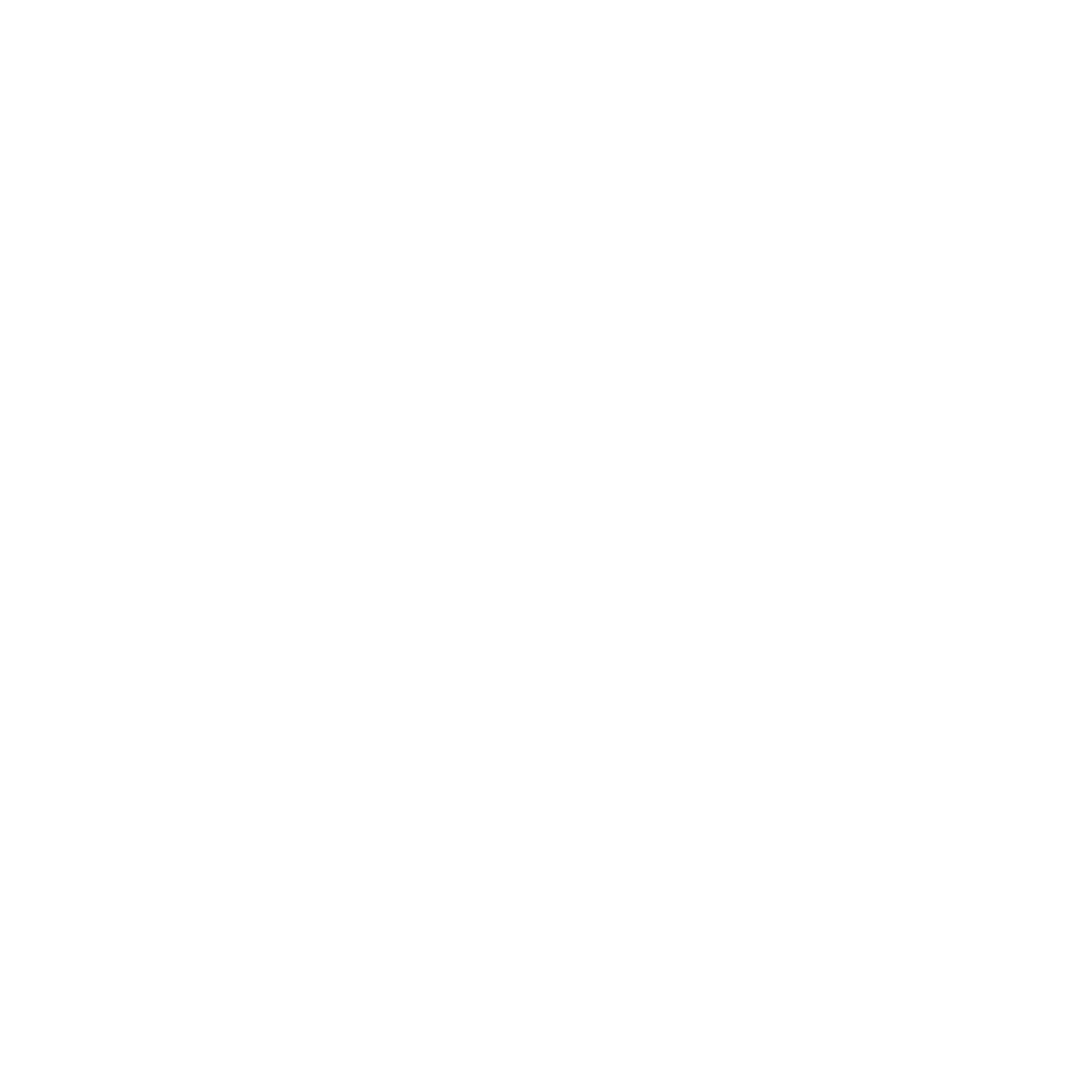
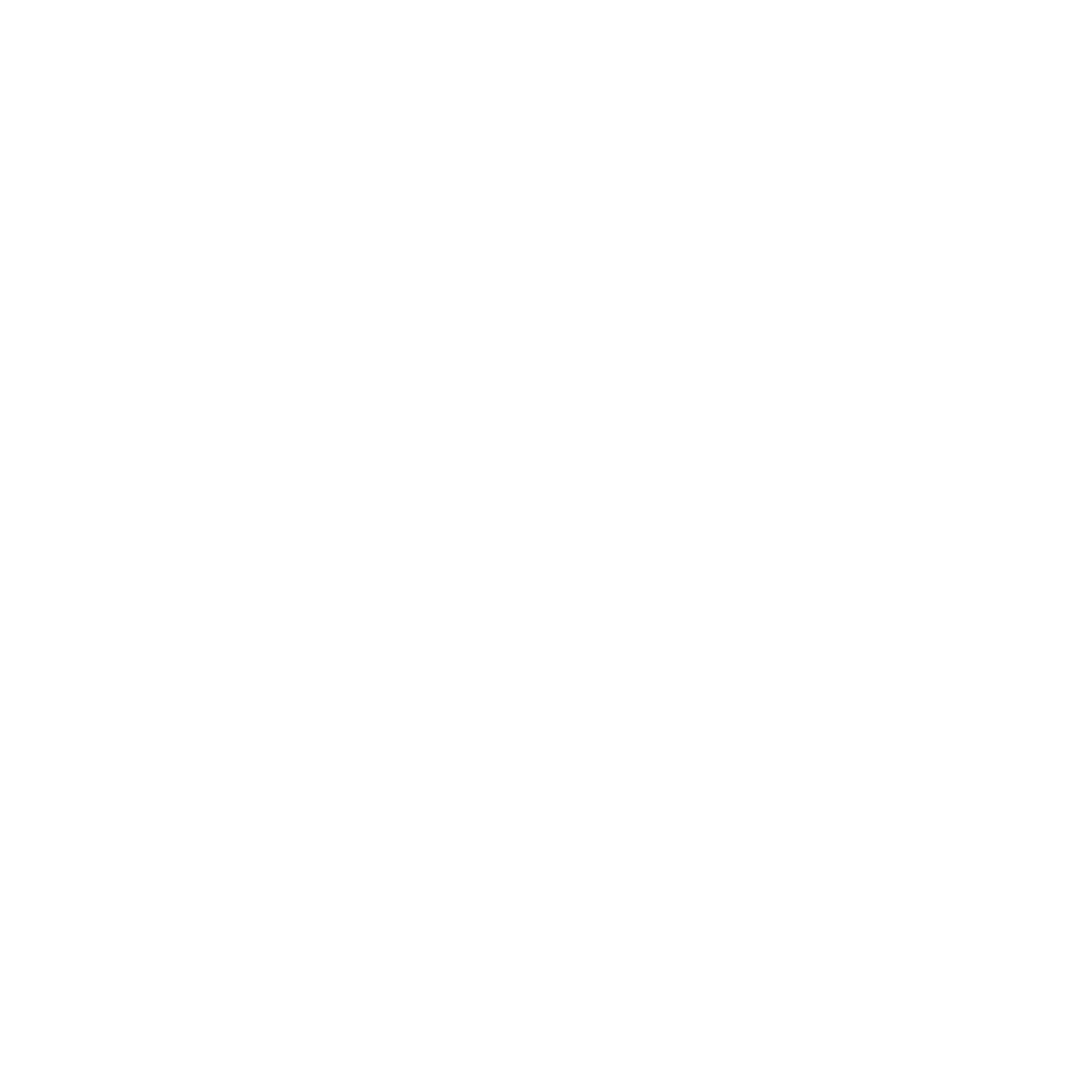
Product Brochures
Get a copy of WARDJET's latest product brochure. Learn all about our extensive range of WARDJet CNC waterjets. Choose between our 6 big series - A-Series, X-Series, M-Series, H-Series, J-Series, and L-Series.